Vacuum Belt Dryer: Principle of Operation
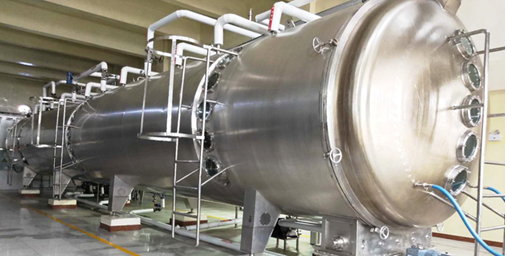
Vacuum belt dryer is continuous infeed and discharge vacuum drying equipment. According the characteristic of the drying product, there are mainly two types of vacuum belt dryer, one is for liquid and paste material, which is conveyed into dryer tube body by infeed pump, evenly spread on belts by distribution device. Under high vacuum, the boiling point of the liquid is lowered; water in the liquid material is evaporated. Belts move on the heating plates evenly. Steam, hot water, hot oil can be used as heating media. With the moving of the belts, the product goes through from the beginning evaporating, drying, and cooling to discharging in the end. The temperature decreases through this process, and can be adjusted for different products. Special vacuum crusher is equipped at the discharge end to produce different size end product. The dry powder or granule product can be automatically packed or continue with subsequent process.
Another is for powder & particle material, there are 3-11 layers of conveyor belts inside the cylindrical shell, the more the layers, and the larger the capacity. By feed and distributing device, the wet solid material is input continuously, and then distributed evenly on the conveyor belt under vacuum. Motion of the belt stirs the materials constantly, which speeds up evaporation, thus shortens the drying time, and also makes sure homogeneity during drying. The drying temperature and drying time (from feed-in to discharge) are adjustable(20-150℃)(20-80min). If the dried product needs granulation, it can be comminuted under vacuum, no dust flying appears, which increases products’yielding and avoid contamination. The dried product is discharged continuously by vacuum discharging and collecting device. Organic solvent in the wet materials can be recycled by our system, removing pollution problem caused by traditional dryers, and adding profit.
Cabinet Dryer: Principle of Operation
According to the shortcomings of Cabinet Dryer in practical use, such as low heat transfer efficiency, slow drying and large energy consumption, giving a example type of vacuum drying oven is FZG15, which is used for steam heating and vacuum pumped by water ring vacuum pump (2BV5121 0kC00-7p maximum displacement 280m3/h7.5kW). The vacuum degree is maintained between 0.06 MPa and 0.08MPa. Given raw material of traditional Chinese medicine extract, moisture content of 40% ~ 60%. dry a batch of extract (32 dishes about 80kg), need about three days and four nights, both time and energy consumption. In the drying process of vacuum drying oven, convective heat transfer is seriously weakened in the vacuum state, and heat transfer mainly depends on heat conduction and thermal radiation of materials by coils and box walls. But because the temperature is low, the proportion of radiation heat transfer is not large. The proportion of heat conduction is large, but the contact area of material tray and coil is small, and the heat transfer effect is not good. Another reason is that with the drying of the material, the bottom surface is dry and hardened, forming a thermal resistance layer, reducing the heat transfer of the coil and the material tray; The upper surface is stiff, resulting in the internal steam which is not easy to discharge, affecting the drying speed, and when the bubble pressure is large enough to break through the stiff layer, the heating material collapses, resulting in waste. Low heat transfer &efficiency Heat transfer mainly depends on heat conduction, radiation heat transfer is very little, and convective heat transfer is seriously weakened. The contact area between the material tray and the coil is small and the heat transfer effect is not good. According to the theory of heat transfer, heat conduction and radiation are almost unaffected by vacuum, while convective heat transfer decreases with the increase of vacuum.
-Below data was comparison between Cabinet Dryer and Vacuum Belt Dryer, provided by one user’s feedback
Raw Material Information:
Solute content of raw material:60%;Feeding amount per hour:125Kg/hr
Powder output per hour:70Kg/hr
A. Using Cabinet Dryer:
Quantity needed:6 units of Cabinet Dryer
(85trays/unit)
production mode: Batch-type drying
Capacity: Approx 4-6 hours for one batch of finished product, which is 70KG
Heating method:Steam
Consumption of Steam: 55KG per hour for one unit, 6units shall be 330KG
E.g Cost of 1KG steam is US$0.04, 330KGX$0.04=$13.2
Electricity:25KW/unitX6units=150KW per hour
Cost of 1KG electricity is US$0.16, 150KW X$0.16=$24
Total:$37.2
B. Using Vacuum Belt Dryer:
Model:MJY60-6
Quantity needed:1 unit of Vacuum Belt Dryer
production mode: Continuous drying
Capacity: It takes about 1 hour with continuously feed in to dried product which is about 70KG
Heating method of drying:Steam
Consumption of Steam for drying: 80KG per hour for one unit
E.g Cost of 1KG steam is US$0.04, 80KGX$0.04=$3.2
Electricity:55KW per hour
Cost of 1KG electricity is US$0.16, 55KW X$0.16=$8.8
Total:$12
Comparison between vacuum belt dryer and cabinet dryer
Seq | Details | 1unit of Vacuum Belt Dryer | 6 units of Cabinet Dryers |
1 | Production Power(Dried product) | 70Kg/hr | 70Kg/hr |
2 | Production Mode | Continuous | Batch-type |
3 | drying temperature | 30~50°(The material temperature) | 60~80°(The material temperature) |
4 | drying duration | 30~60 minutes | 4~6hours |
5 | Dried product Quality | Stable quality, no damage to the original component | unevenness of drying |
6 | Shape of dried product | Porous particles with good color | Uneven colour, the lump needs to be re-crushed |
7 | The yield of product | ≥ 99% | 85~92% |
8 | Discharge mode | Automatically | Manually |
9 | Crushing mode | Vacuum online | atmospheric pressure,Causing secondary pollution |
10 | Risk of secondary pollution | Low | High |
11 | Active ingredient retention | Good | Ordinary |
12 | Cleaning method | Automatic on-line cleaning (CIP), no dead Angle | Manually cleaning |
13 | Running Cost | Low | High |
14 | operation staff | 1~2 persons | 4~7 persons |
15 | the change of varieties | Short cleaning time &short variety replacement time | Long cleaning time & Long variety replacement time |
16 | Product solubility | Good | Ordinary |
17 | Device Control | Simple | Complicated |
18 | Maintenance | Simple | Ordinary |